working principle of rockwell hardness tester|how to calculate rockwell hardness : mail order The Rockwell hardness test is the industry standard measuring system used to determine how resistant a material is to another object. Hardness is defined as a material’s resistance to permanent indentation. webDefinition of survive. 1. as in to endure. to come safely through the cat miraculously survived a two-story fall. Synonyms & Similar Words. Relevance. endure. live. withstand. make it (through) be. weather. ride (out) continue. thrive. exist. outlive. outlast. persist. last. subsist. wear out. stand. hold out. prosper. breathe. abide. flourish.
{plog:ftitle_list}
WEBFull length You Broke It! with Johnny Love, Ashlyn Peaks in HD on RealityKings.com. Watch now and see our thick Johnny Love, Ashlyn Peaks getting fucked hard!
What is the Principle of the Rockwell Method? You can think of the Rockwell Hardness method as an impact-dependent hardness measuring method. The reason is that it requires an indenter with a known diameter and a specified load to impact the surface of the .Theory and Principle of the Rockwell Hardness Test The Rockwell Hardness .Principle of Test. The Rockwell test consists of measuring the additional depth to which a carbide ball or Brale® diamond penetrator is forced by a heavy (major) load beyond the .Indentation hardness value is obtained by measuring the depth or the area of the indentation using one of over 12 different test methods. Learn more about hardness testing basics here. The Rockwell hardness test method, as defined .
The Rockwell hardness test is the industry standard measuring system used to determine how resistant a material is to another object. Hardness is defined as a material’s resistance to permanent indentation.
Theory and Principle of the Rockwell Hardness Test The Rockwell Hardness Test uses a depth-differential method to test for hardness. A predetermined minor load is applied to the test . The Rockwell hardness test involves making an indentation on the test material. The indenter is either a conical diamond or a steel ball. Indenter ball diameters range from 1/16 to 1/2 inches and are chosen based .The Rockwell hardness test, how does it work? Principle, application, hardness scales, minimum thickness, repeatability and error..
In the Rockwell hardness test, the measure of the hardness is not an indentation surface but an indentation depth. Either a carbide ball or a rounded diamond cone with a tip angle of 120° and a tip radius of 0.2 mm .
This article discusses methods and the principles behind hardness testing. Hardness testing may not be a fundamental physical property, but that does not mean it is not an important property to test and . ASTM E10: This standard covers Brinell hardness testing in metallic samples. ASTM E18: This standard includes the various ways that Rockwell hardness can be measured by standard methods, specifically for .ACKNOWLEDGMENTS Theauthorwouldliketothankthefollowingpersonsforsharingtheir experienceandprovidinginformationforthisGuide.Theirinputandreview .Principle of Rockwell hardness testing . The Rockwell hardness test is one of several common indentation hardness tests used today, other examples being the Brinell hardness test and Vickers hardness test. Most indentation hardness tests are a measure of the deformation that occurs when the material under test is penetrated with a specific type .
Conventional hardness testers, like Rockwell, Brinell or Vickers machines, require the test piece be brought to the testing device; but this is not always possible. Portable testing devices have been developed that permit in-situ hardness measurements thus offering quick and economical supplements to conventional, stationary testing machines.Testing Principle. The Rockwell hardness test measures hardness based on the depth of penetration of an indenter under a specific load. It utilizes two types of indenters: a diamond cone for harder materials and a steel ball for softer materials. The test measures the difference in depth between the initial and final indentation after applying .The Rockwell hardness test. Rockwell is a fast hardness test method developed for production control, with a direct readout, mainly used for metallic materials. The Rockwell hardness (HR) is calculated by measuring the depth of an indent after an indenter has been forced into the specimen material at a given load.How Does Hardness Testing Work? The mechanism of hardness testing involves applying a standardized, rigid tool known as an indenter onto the material under examination. . For instance, in the Rockwell hardness test, hardness values range from 0 to 100 based on indentation depth, but each test method defines its scale uniquely.
Advantages of Rockwell Hardness Test. Typically, the Rockwell test is easy to execute and more precise than other kinds of hardness evaluations. The Rockwell test technique is used on all metals, except when the test would introduce too many surface variations; when indentations would be too large; or where the sample otherwise prohibits its use.
rockwell hardness tester diagram
rockwell hardness test explained
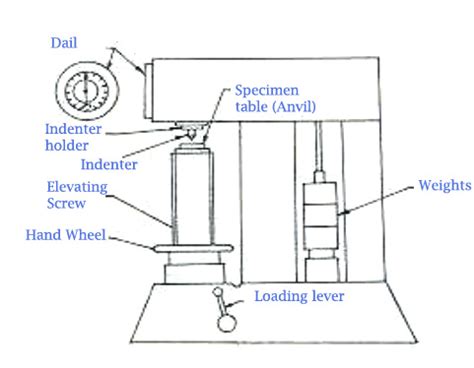

The Rockwell method is a static hardness testing method, which can be further characterised as follows: It is one of the standardised procedures (ISO 6508, ASTM E18). The process is used to test hardness in the macro range (test force >= 49.03 N), more precisely with a test force of 29.42 to 1471 N. It is a differential-depth method.
Working Principles of Micro Hardness Testing. . Vickers, and eventually Rockwell hardness tests. Micro hardness testing still employs indentation to probe the surface of a sample and measure the resulting impression. The principles vary from test-to-test, but – typically – a sample is placed on a piezo-driven stage and positioned below a .
Learn all you need to know about Rockwell hardness testing – including test definitions, test calculations and insight into Rockwell hardness testing machines and HRC hardness testers – with knowledge and expertise from Struers, the world’s leading materialographic and metallographic experts. . Designed to work with a dedicated .
What is Rockwell hardness testing? The Rockwell Hardness Test is generally a non-destructive test performed on samples when it’s necessary to determine how hard a material is. It’s generally considered easier to perform compared to other methods, like Vickers or Brinell hardness testing. Another advantage is the small area of indentation needed to carry out the .
this: Rockwell hardness testers are usually less costly than optical hardness testers, the test itself is quick and easy, surface finish of the material is not critical, and the Rockwell scale is a commonly . 2.3 Functional and Calculation Principle for Brinell Sample Surface Force (F) HBW = Brinell Hardness HBW = Constant x HBW = 0.102 x d 1 .A Vickers hardness tester. The Vickers hardness test was developed in 1921 by Robert L. Smith and George E. Sandland at Vickers Ltd as an alternative to the Brinell method to measure the hardness of materials. [1] The Vickers test is often easier to use than other hardness tests since the required calculations are independent of the size of the indenter, and the indenter .A Rockwell hardness tester is designed to test the hardness of materials using the differential depth method. A typical Rockwell hardness testing machine consists of a load application feature, an indenter, a test anvil and a . Hardness generally refers to the resistance of a material to scratching or indentation, and a qualitative measure of the strength of the material. The most commonly used hardness tests are the Rockwell test, Brinell test and the Vickers hardness test. This article will provide an introduction into durometer hardness and the gauge used to .
Variants on the Rockwell hardness test procedure are used depending on the material and strength of a part. The most common Rockwell variants include: HRC – Known as “Rockwell C,” a 150 kgf load is applied via a diamond in this method.Rockwell hardness testing is a method that determines the hardness of metals and polymers, and it is very common in most metallurgy and metal forging industry activities. Hardness testing does not test performance attributes. Yet, a material’s hardness correlates with its strength, wear resistance, and other properties. .
Hardness testing is of immense importance for quality assurance in industry. Although the most widely used hardness test methods for metals—Rockwell, Brinell, and Vickers—were developed between 1900 and 1925, numerous technical innovations have been made in recent years, leading to an increase in productivity and the accuracy of hardness tests.This article will first introduce the working principles, advantages, and limitations of the Rockwell and Vickers hardness tests, respectively. Next, we will focus on the in-depth discussion of the differences between each testing method. . Rockwell Hardness Test: Hardness is calculated by applying a load to the surface of the test material . There are many types of hardness testers, the most commonly used Rockwell, Brinell, Vickers and microhardness testing methods. Rockwell hardness measurement is one of the most commonly used hardness testing methods. It is represented by the plastic deformation of the pressed material under the action of the indenter (d
The Rockwell hardness test is one of several common indentation hardness tests used today, other . “Dynamic Impact” is based on the Leeb principle of hardness,developed by Dietmar Leeb in the 1970’s. A spring loaded impact body is thrust to the test surface, effecting rebound. The speed of both the initial Hardness testers are complex in design but simple in principle, operation and application. . describing how they work and their suitability for differing applications. 1. Rockwell Hardness Testers. Rockwell hardness testers are the most commonly used of all the types of hardness testers. The Rockwell method offers a quick and accurate measure .CV-600A Rockwell hardness tester is an universalized apparatus for Rockwell hardness detemination. It can be used in the test of Rockwell hardness of various materials. The applying speed of test pressure can be adiusted by a buffering device, and the change of pressure is obtained by turning of a pressure selecting handwheel.

(4) Selection of F and D (principle of geometric similarity of indentation) When measuring Brinell hardness with indenters of different diameters and loads of different sizes, the principle of geometric similarity must be met to obtain the same HB value, that is, the opening angleφ of the indentation is equal.. Method: The same HB shall be measured for samples with .
rockwell hardness test diagram
rockwell hardness test calculation
WEBUma última como se chama quando a gente exagera para conseguir passar uma ideia. Por exemplo, quando a gente diz que chorou um rio de lagrimas ou repetiu a coisa mil vezes. A. Um eufemismo. B. Uma enfase. C. Uma hipérbole (Resposta certa) Espero .
working principle of rockwell hardness tester|how to calculate rockwell hardness